Addressing Challenges In Automated Visual Inspection Of Lyophilized Vials
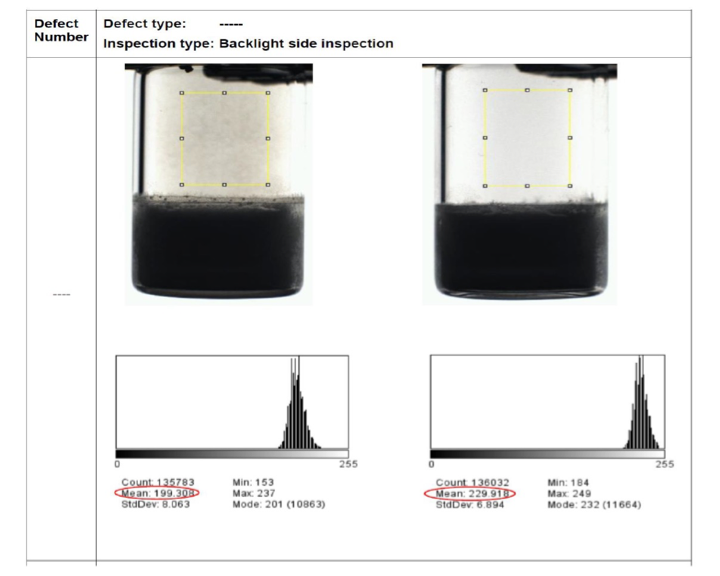
Table of Contents
Challenges Related to Image Acquisition and Processing
The inherent variability of lyophilized cakes significantly impacts the effectiveness of automated visual inspection. Consistent image acquisition and reliable defect detection are hindered by several factors.
Variations in Lyophilized Cake Appearance
The appearance of a lyophilized cake can vary considerably depending on numerous factors, making consistent automated inspection difficult. These variations pose significant challenges for image processing algorithms.
- Variations in cake shape, size, and color: Cakes can differ in size and shape, and subtle color variations can occur due to differences in formulation or the lyophilization process itself.
- Presence of cracks, fissures, or collapses: These defects can range from minor imperfections to significant structural failures, requiring sensitive detection capabilities.
- Differences in opacity and texture: The degree of opacity and surface texture can vary, affecting light reflection and scattering, impacting image analysis algorithms.
- Impact of vial type and fill volume on image consistency: Different vial types and fill volumes can affect how light interacts with the cake, further complicating image analysis.
Creating consistent image acquisition parameters is difficult due to this inherent variability. Image analysis algorithms struggle to differentiate between acceptable variations and actual defects. Techniques like standardized lighting, carefully controlled temperature and humidity during imaging, and advanced image pre-processing techniques like image normalization are crucial to mitigate these challenges. Implementing robust image processing algorithms and machine vision techniques are key to improving the accuracy of defect detection.
Dealing with Reflections and Glare
Reflections from the vial glass and glare from the lyophilized cake surface are major obstacles in automated visual inspection. These artifacts can mask genuine defects, leading to false negatives.
- Reflections from the vial glass: The curved surface of the vial can create reflections that obscure the cake's appearance.
- Glare from the lyophilized cake surface: The cake's surface can reflect light, creating glare that makes defect detection difficult.
- Impact of lighting conditions and vial orientation: The angle and intensity of the light source significantly impact reflections and glare.
Differentiating between genuine defects and artifacts requires sophisticated image processing techniques. Advanced lighting techniques such as structured lighting, the use of polarization filters to reduce glare, and sophisticated algorithms specifically designed for reflection reduction and glare mitigation are essential. These advanced imaging techniques can significantly improve the accuracy and reliability of automated visual inspection systems.
Subtle Defect Detection
Identifying small particles, minute cracks, or other subtle defects presents a significant challenge for automated systems. The sensitivity of current systems may be insufficient to reliably detect these critical defects.
- Identification of small particles: Small particles within the lyophilized cake can indicate contamination and must be reliably detected.
- Detection of minute cracks: Microscopic cracks might not be visible to the naked eye but can compromise the integrity of the product.
- Differentiating between acceptable variations and critical defects: The system must be able to distinguish between harmless variations and defects that affect product quality and safety.
High-resolution imaging, combined with advanced algorithms like deep learning, is crucial for enhancing the sensitivity of automated visual inspection. Deep learning algorithms can be trained on extensive datasets of images to learn complex patterns and identify subtle defects that might be missed by conventional methods. In some cases, combining visual inspection with other analytical techniques can provide a more comprehensive assessment of product quality. This approach can significantly improve particle detection, crack detection, and overall sensitivity enhancement.
Challenges Related to System Integration and Validation
Integrating automated visual inspection systems into existing production lines and ensuring regulatory compliance are crucial considerations.
Integration with Existing Production Lines
Integrating AVI systems into existing production lines requires careful planning and consideration of various factors.
- Compatibility with existing equipment: The system must be compatible with the existing equipment and infrastructure.
- Throughput requirements: The system must be able to inspect vials at the required throughput to avoid production bottlenecks.
- Integration challenges with upstream and downstream processes: Seamless integration with upstream and downstream processes is essential for efficient workflow.
System integration should prioritize speed and accuracy without compromising the overall production efficiency. Careful consideration of throughput optimization and automation are crucial aspects of successful system integration.
Validation and Regulatory Compliance
Validation is critical to ensure the accuracy and reliability of automated visual inspection systems, and compliance with regulatory requirements is paramount.
- Meeting regulatory requirements (e.g., FDA 21 CFR Part 11): The system must comply with all relevant regulatory requirements.
- Validation of system accuracy and reliability: Rigorous testing and validation are necessary to demonstrate the accuracy and reliability of the system.
- Demonstrating consistent performance over time: The system's performance must remain consistent over time, and this must be demonstrably verifiable.
Validation and regulatory compliance require a meticulous approach, involving rigorous testing, comprehensive documentation, and adherence to guidelines like FDA 21 CFR Part 11. Consistent system performance verification is crucial for maintaining compliance and ensuring product quality and safety.
Conclusion
Automated visual inspection of lyophilized vials offers significant advantages in quality control, but successful implementation requires addressing several critical challenges. Overcoming challenges related to image acquisition, processing, and system integration demands a multifaceted approach, combining advanced imaging technologies, sophisticated algorithms, and meticulous validation procedures. By strategically addressing these challenges, pharmaceutical manufacturers can leverage the benefits of automated visual inspection to ensure consistent product quality and meet stringent regulatory requirements. To learn more about optimizing your automated visual inspection of lyophilized vials and improving your lyophilization process, contact us today.
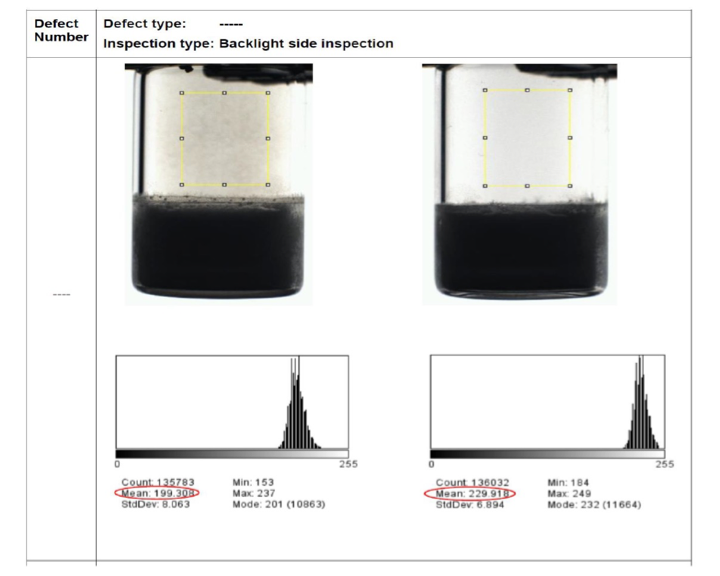
Featured Posts
-
Amazon Boss Jeff Bezos James Bond Poll The Fans Have Spoken
May 11, 2025 -
Amsterdam Cafes Kings Day Mural A Homage To Artist Marjolein Faber And Her Ribbon Gate
May 11, 2025 -
Chantal Ladesou Les Vraies Raisons De Son Absence Du Jeu Qui Rit Sort
May 11, 2025 -
Ufc 315 In Depth Predictions And Betting Odds For Shevchenko Vs Fiorot
May 11, 2025 -
Princess Beatrice On Her Parents Divorce A Candid Reflection
May 11, 2025