Automated Visual Inspection Of Lyophilized Products: A Focus On Challenges And Solutions
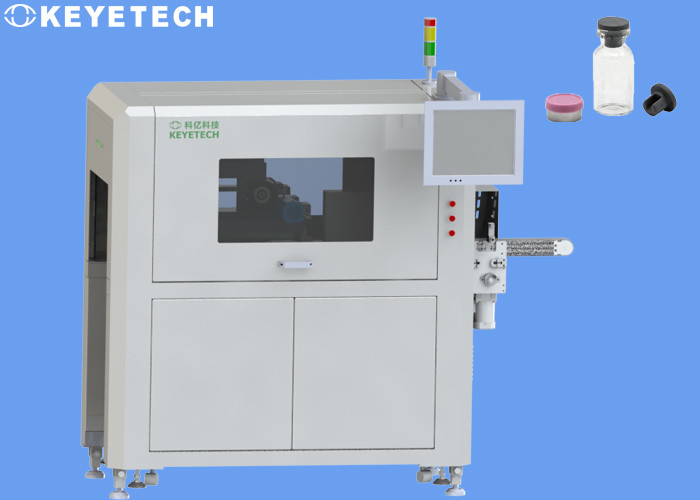
Table of Contents
Challenges in Manual Visual Inspection of Lyophilized Products
Manual visual inspection of lyophilized products, while seemingly straightforward, presents several significant hurdles that impact both product quality and operational efficiency.
Subjectivity and Variability
Human inspectors, despite rigorous training, introduce subjectivity into the inspection process. This leads to variability in results, creating inconsistencies that undermine data reliability.
- Differences in inspector training: Variations in training programs can result in differing interpretations of acceptable quality standards.
- Inspector fatigue: Prolonged visual inspection can lead to fatigue, reducing accuracy and increasing the likelihood of missed defects.
- Individual interpretation: Subtle defects, such as hairline cracks or minor discoloration, can be interpreted differently by different inspectors.
These inconsistencies create significant challenges in maintaining regulatory compliance and ensuring consistent product quality. Data collected from manual inspections may lack the reliability needed for robust statistical process control and trend analysis.
Time-Consuming and Labor-Intensive Process
Manual inspection is a slow and labor-intensive process, creating significant bottlenecks in the production line.
- Bottlenecks in production: The time required for manual inspection can significantly delay overall production throughput.
- Increased processing time: Increased processing time leads to higher production costs and longer lead times for product delivery.
- Higher labor expenses: Manual inspection requires a substantial workforce, contributing significantly to labor costs.
The high labor costs and reduced efficiency associated with manual inspection directly impact overall production profitability.
Difficulty in Detecting Subtle Defects
The human eye has limitations, especially when it comes to detecting small, subtle defects in lyophilized products.
- Microscopic cracks: Hairline cracks may be undetectable to the naked eye, but can compromise product integrity.
- Minor discoloration: Slight changes in color may indicate degradation or contamination, but can easily be missed during manual inspection.
- Foreign particles: Small foreign particles can be difficult to spot without magnification.
Failing to detect these subtle defects can have serious consequences, leading to product recalls, patient safety risks, and significant financial losses.
Implementing Automated Visual Inspection Systems for Lyophilized Products
Automated visual inspection systems offer a robust solution to the challenges associated with manual inspection, leveraging advanced technologies to enhance accuracy and efficiency.
Technology Options
Several technologies are available for automated visual inspection of lyophilized products, each with its own strengths and weaknesses:
- Machine vision systems: These systems use cameras and sophisticated image processing algorithms to analyze images of lyophilized products, identifying defects based on predefined criteria. They offer high speed and accuracy.
- AI-powered image analysis: Artificial intelligence and machine learning algorithms can be used to further enhance the capabilities of machine vision systems, allowing for the detection of more subtle defects and improved classification of defect types. This can lead to significant improvements in sensitivity and specificity.
- Spectroscopic techniques: Techniques like near-infrared (NIR) spectroscopy can be integrated to provide additional information about the chemical composition and structural integrity of the lyophilized product, further improving defect detection.
The choice of technology depends on factors such as the type of defects to be detected, the throughput requirements, and the budget.
System Integration and Validation
Integrating automated visual inspection systems requires careful planning and execution. This process involves:
- System qualification: Verifying that the system is installed and operating according to specifications.
- Performance verification: Demonstrating that the system meets the required performance standards for defect detection.
- Regulatory compliance: Ensuring that the system complies with relevant regulations, such as 21 CFR Part 11 for electronic records and signatures.
Proper validation is crucial to ensure the reliability and accuracy of the inspection data and demonstrate compliance to regulatory bodies.
Data Management and Analysis
Automated systems provide comprehensive data management and analysis capabilities:
- Detailed defect reports: Automated systems can generate detailed reports on the types and frequency of defects detected.
- Real-time data visualization: Data can be visualized in real-time, allowing operators to monitor the quality of the product and identify potential issues immediately.
- Integration with other systems: Data can be integrated with other quality control systems, facilitating trend analysis and process improvement initiatives.
Data-driven decision making enables proactive identification of root causes of defects and implementation of targeted corrective actions.
Overcoming Implementation Hurdles in Automated Visual Inspection
While automated visual inspection offers numerous advantages, there are some hurdles to consider:
Cost of Implementation
The initial investment for automated systems can be substantial. However, the long-term benefits often outweigh the initial cost.
- Cost considerations: Factors like system hardware, software, installation, validation, and training need to be factored into the overall cost.
- Return on investment (ROI): The ROI on automated visual inspection should be carefully assessed, considering factors such as reduced labor costs, improved efficiency, and minimized product recalls.
- Long-term cost savings: The reduction in labor costs, improved efficiency, and minimized product recalls can lead to significant cost savings in the long run.
System Training and Maintenance
Proper training and ongoing maintenance are crucial for the successful implementation of automated visual inspection systems.
- Operator training: Operators need to be trained on how to operate and maintain the system, interpret the data, and troubleshoot any issues.
- Preventative maintenance: Regular preventative maintenance helps to ensure the continued reliable operation of the system.
- Troubleshooting procedures: Having clear troubleshooting procedures in place is crucial for minimizing downtime.
Data Integration and Compatibility
Integrating automated systems with existing manufacturing information systems can present challenges:
- Data formats: Ensuring compatibility between the data formats used by the automated system and other systems.
- Compatibility issues: Addressing any compatibility issues that may arise between the automated system and other software and hardware.
- Potential solutions: Implementing standard data formats and using appropriate integration tools can help overcome these challenges.
Conclusion: The Future of Automated Visual Inspection for Lyophilized Products
Automated visual inspection offers a significant advancement in lyophilized product quality control. By addressing the limitations of manual inspection, such as subjectivity, time constraints, and the difficulty in detecting subtle defects, automated systems significantly enhance the accuracy, efficiency, and reliability of the inspection process. This leads to improved product quality, enhanced patient safety, and reduced operational costs. While the initial investment can be substantial, the long-term benefits—including reduced labor costs, minimized recalls, and improved overall efficiency—make automated visual inspection a strategic investment for any lyophilized product manufacturer. Invest in automated visual inspection today to elevate your lyophilized product quality control and improve operational efficiency.
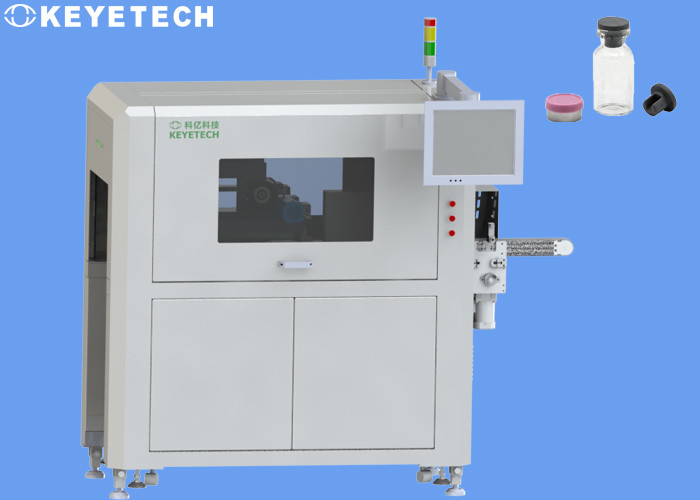
Featured Posts
-
The 10 Best John Wick Inspired Action Movies
May 11, 2025 -
Netherlands Plans Area Bans For Troublesome Asylum Seekers
May 11, 2025 -
The China Factor Analyzing Challenges For Premium Auto Brands Like Bmw And Porsche
May 11, 2025 -
Tensions Flare Belal Muhammad And Jack Della Maddalenas Heated Exchange At Ufc 315
May 11, 2025 -
The Graham Rahal 911 Gt 3 Rs 4 0 Performance Rarity And Driving Excellence
May 11, 2025