Automated Visual Inspection Of Lyophilized Vials: Challenges And Solutions
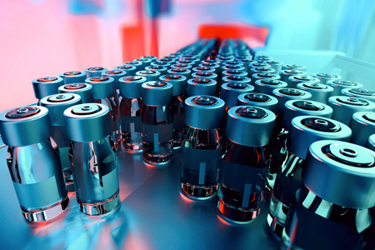
Table of Contents
Challenges in Automated Visual Inspection of Lyophilized Vials
Automated visual inspection of lyophilized vials presents unique hurdles due to the inherent complexities of the product and the stringent quality control requirements. Several key challenges need to be addressed for successful implementation.
Variability in Lyophilized Cake Appearance
The lyophilization process, while crucial for preserving the product's stability, can lead to variations in the appearance of the lyophilized cake. These variations can include:
- Cracks: Fine cracks or fissures on the cake surface.
- Collapse: Partial or complete collapse of the cake structure.
- Discoloration: Subtle changes in color or shading.
These variations can be subtle and difficult to distinguish from actual defects using traditional visual inspection methods. This necessitates high-resolution imaging and sophisticated algorithms capable of differentiating acceptable variations from critical defects impacting product quality and efficacy. The challenge lies in setting accurate thresholds to avoid false positives and ensure reliable detection of genuine defects in automated lyophilized vial inspection.
Contamination Detection
Detecting particulate matter, foreign bodies, and other forms of contamination is paramount for ensuring the safety and efficacy of lyophilized products. However, several challenges arise:
- Differentiation from Artifacts: Distinguishing true contamination from harmless artifacts or shadowing effects can be difficult.
- Microscopic Contaminants: Detecting tiny particles requires sensitive lighting and advanced image processing techniques.
- Handling Procedures: Even the most advanced systems can be hindered by inadequate cleaning and handling procedures upstream in the manufacturing process.
Effective contamination detection demands sensitive lighting strategies like dark-field illumination, which enhances contrast and visibility of small particles against the lyophilized cake. Advanced algorithms are needed to analyze images and accurately flag potential contaminants, reducing the risk of releasing compromised products.
High-Throughput Requirements
Pharmaceutical manufacturing operates under strict timelines and high-volume production demands. This translates to a crucial need for high-throughput automated visual inspection systems:
- Speed and Accuracy: Balancing inspection speed with accuracy is crucial to avoid bottlenecks without compromising quality control.
- System Reliability: Automated systems must be robust and reliable, minimizing downtime and ensuring consistent performance.
- Integration with Production Lines: Seamless integration with existing production lines is essential for optimal efficiency and minimizing disruption.
Meeting these high-throughput requirements demands the use of advanced robotic systems and parallel processing techniques for analyzing images swiftly and accurately. Robust quality control systems and preventive maintenance protocols are essential to mitigate potential system failures and maintain the necessary throughput.
Solutions for Efficient Automated Visual Inspection
Addressing the challenges of automated visual inspection of lyophilized vials requires a multi-pronged approach focusing on technological advancements and streamlined integration:
Advanced Imaging Technologies
The core of effective automated visual inspection lies in leveraging advanced imaging technologies:
- High-Resolution Cameras: High-resolution cameras capture detailed images of the vials, crucial for identifying subtle defects.
- Multispectral Imaging: This technique uses multiple wavelengths of light to reveal features invisible under standard illumination.
- 3D Imaging: 3D imaging techniques provide a more comprehensive assessment of the lyophilized cake's structure and integrity, aiding in the detection of internal defects.
- Lighting Techniques: Optimizing lighting is critical. Dark-field and bright-field illumination, along with other advanced techniques are used to enhance the visibility of defects.
The choice of imaging modality depends on the specific requirements and the types of defects to be detected. Careful consideration and testing are required to select the most suitable technology.
Sophisticated Image Processing Algorithms
Advanced image processing algorithms are essential for automated defect classification and identification:
- Machine Learning & AI: Machine learning and artificial intelligence algorithms are increasingly used to analyze vial images and identify defects with high accuracy. These algorithms learn from large datasets of vial images and continuously improve their detection capabilities.
- Algorithm Training: Regular training and updates are necessary to adapt algorithms to variations in lyophilization processes and to improve their performance over time.
- Robustness: Algorithms must be robust to variations in lighting, background, and vial orientation, ensuring consistent performance across different batches and conditions.
The development and implementation of these sophisticated algorithms are crucial for the success of any automated visual inspection system.
Integration with Existing Systems
Seamless integration with existing systems is crucial for efficient operation and compliance:
- Production Line Integration: The automated system should integrate seamlessly with existing filling lines and other production equipment, minimizing downtime and operational disruptions.
- Data Analytics: Data analytics tools provide insights into the inspection process and allow for process optimization and predictive maintenance.
- Data Management & Traceability: Effective data management and traceability are crucial for regulatory compliance and ensuring product quality.
- Real-time Feedback: Real-time feedback mechanisms allow for immediate adjustments to the production process based on inspection results.
A well-integrated automated visual inspection system improves overall production efficiency, minimizes waste, and provides valuable data for continuous improvement.
Conclusion
Automated visual inspection of lyophilized vials presents unique challenges due to the delicate nature of the product and the need for high throughput. However, by implementing advanced imaging technologies, sophisticated image processing algorithms, and efficient system integration, these challenges can be effectively addressed. The adoption of automated visual inspection systems ultimately leads to improved product quality, increased efficiency, reduced costs, and enhanced regulatory compliance. Investing in and optimizing your automated visual inspection system is vital for success in the pharmaceutical industry. Learn more about optimizing your automated visual inspection of lyophilized vials today!
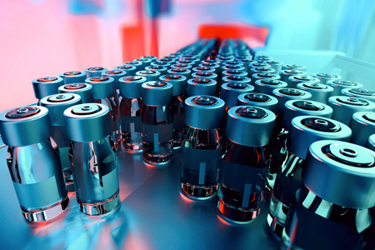
Featured Posts
-
Semana Santa O Semana De Turismo El Significado Detras Del Nombre En Uruguay
May 11, 2025 -
Post Match Reaction Sheehan Addresses Ipswich Towns Performance
May 11, 2025 -
La Fire Aftermath Price Gouging Concerns Raised By Selling Sunsets Stars Name
May 11, 2025 -
Accidental Reveal Selena Gomez And Benny Blancos Private Life
May 11, 2025 -
Kim Kardashi An Stilska Kreatsi A Ko A Gi Potentsira Ne Zinite Atributi
May 11, 2025