Challenges And Advancements In Automated Visual Inspection Of Lyophilized Pharmaceuticals
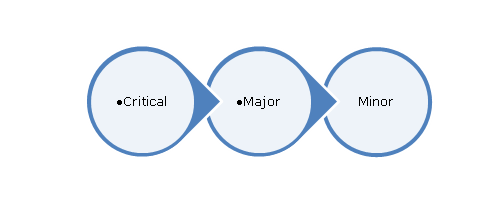
Table of Contents
Challenges in Automated Visual Inspection of Lyophilized Pharmaceuticals
Automating the visual inspection of lyophilized pharmaceuticals presents unique hurdles. The inherent complexities of these delicate products necessitate sophisticated solutions.
Variability in Lyophilized Product Appearance
- Diverse cake structures: Lyophilized products exhibit a wide range of cake structures, from dense and compact to porous and fragile. This variability makes consistent defect identification challenging.
- Cracking and collapse: Cracks, collapses, and other structural defects are common in lyophilized pharmaceuticals, and their detection requires algorithms capable of identifying subtle variations in surface texture and morphology.
- Color and texture variations: Slight variations in color and texture can be inherent to the lyophilization process and may not always indicate a defect. Distinguishing between acceptable variations and actual defects requires advanced image analysis techniques.
- Subjectivity in human inspection: The subjectivity inherent in manual inspection makes it difficult to establish clear, objective defect criteria for automated systems. This necessitates the development of robust algorithms that can account for this inherent variability.
The inherent variability in lyophilized product appearance presents a significant challenge for automated visual inspection. Factors like variations in freeze-drying processes, formulation, and storage conditions contribute to this heterogeneity. Sophisticated image analysis techniques, including advanced algorithms and machine learning, are crucial to differentiate between acceptable variations and actual defects.
Contamination Detection
- Particulate matter: Identifying small particles, foreign bodies, and other contaminants within the often-translucent lyophilized cakes requires high-resolution imaging capabilities.
- Optical artifacts: Differentiating between true contamination and optical artifacts like shadows or reflections is crucial to prevent false positives and maintain high accuracy.
- Robust lighting: The lighting system employed is crucial. Uniform and optimized lighting minimizes shadows and enhances contrast, aiding in the detection of even minute contaminants.
- Image pre-processing: Pre-processing techniques are essential to filter out noise and artifacts, improving the overall image quality and enhancing the detection of contaminants.
Detecting minute contaminants against the lyophilized cake’s background is a significant challenge. Advanced imaging techniques like hyperspectral imaging or multispectral imaging are increasingly explored to improve contrast and accuracy in contamination detection. These techniques provide spectral information beyond the visual spectrum, significantly improving the sensitivity of contaminant detection.
System Integration and Validation
- Production line integration: Integrating automated visual inspection systems into existing pharmaceutical production lines requires careful planning and consideration of factors like throughput and system compatibility.
- Regulatory compliance: Compliance with stringent regulatory standards, such as those set by the FDA and EMA, is paramount. This includes rigorous validation protocols to demonstrate the accuracy and reliability of the automated system.
- Data management: Effective data management systems are essential for tracking inspection data, facilitating trend analysis, and ensuring regulatory compliance. These systems help identify potential problems in the production process and improve overall quality control.
- Validation protocols: Thorough validation protocols must be established to demonstrate the automated system’s accuracy and reliability, ensuring it meets the stringent requirements for quality and reliability in pharmaceutical manufacturing.
Successful integration of automated visual inspection necessitates careful planning. Considerations include throughput, system compatibility with existing equipment, and robust data management. Validation, crucial for demonstrating compliance with regulatory standards (e.g., FDA 21 CFR Part 11), ensures that the automated system functions as intended and maintains high levels of accuracy and reliability.
Advancements in Automated Visual Inspection of Lyophilized Pharmaceuticals
Significant advancements are driving progress in automated visual inspection, leading to more efficient and accurate quality control.
Advanced Image Processing Techniques
- Machine learning (ML) and artificial intelligence (AI): AI and machine learning algorithms are revolutionizing defect detection and classification. These algorithms learn from extensive image datasets, improving accuracy over time.
- Deep learning models: Deep learning models excel at automated feature extraction and pattern recognition, identifying subtle defects often missed by traditional methods.
- Computer vision techniques: Computer vision techniques enhance image quality, improving the accuracy of defect detection and minimizing false positives.
Advancements in image processing are paramount. AI and machine learning provide the ability to learn from vast datasets, resulting in systems that adapt and improve over time. Deep learning models are particularly effective in identifying subtle defects often missed by conventional methods.
High-Resolution Imaging Technologies
- High-resolution cameras: High-resolution cameras capture detailed images, enabling the detection of even minute defects.
- Advanced lighting techniques: Optimized lighting techniques minimize shadows and enhance contrast, improving the visibility of defects.
- Specialized imaging systems: Specialized imaging systems are being developed specifically to address the unique challenges of inspecting lyophilized pharmaceuticals.
- Hyperspectral and multispectral imaging: These emerging technologies offer enhanced defect detection capabilities by providing spectral information in addition to visual data.
Improved imaging technologies are crucial for achieving high accuracy. Higher resolution cameras and optimized lighting substantially enhance the detection of subtle defects. Emerging technologies, such as hyperspectral and multispectral imaging, offer the potential for even greater accuracy and sensitivity.
Improved Data Analysis and Reporting
- Sophisticated data analysis tools: Advanced data analysis tools efficiently interpret inspection results, providing actionable insights into the production process.
- Detailed reports for regulatory compliance: The systems generate detailed reports for regulatory compliance and quality assurance purposes. This ensures traceability and accountability.
- Data management systems: Integration with data management systems allows for tracking inspection data, enabling trend analysis to identify and address potential issues proactively.
Effective data analysis and management are vital for leveraging the information from automated inspection. Sophisticated software is necessary to analyze large datasets, enabling efficient identification of trends and potential issues within the production process. Detailed reports are crucial for both regulatory compliance and ensuring high-quality assurance.
Conclusion
Automated visual inspection of lyophilized pharmaceuticals presents considerable challenges, yet recent advancements in imaging technologies, AI, and data analysis are revolutionizing quality control processes. By addressing the variability in product appearance, improving contamination detection, and streamlining system integration, the pharmaceutical industry can achieve greater efficiency, accuracy, and regulatory compliance. Embracing these advancements in automated visual inspection systems is crucial for maintaining the consistent high quality of lyophilized pharmaceuticals. Invest in advanced automated visual inspection solutions to enhance your quality control processes and improve the safety and efficacy of your lyophilized pharmaceuticals.
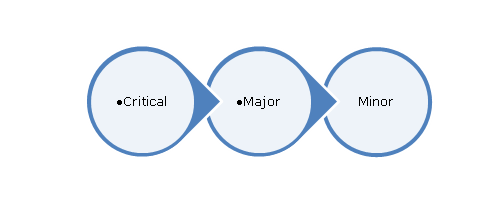
Featured Posts
-
One Loss Twelve Wins The Rise Of Manon Fiorot In Mma
May 12, 2025 -
Possible Candidates For The Next Pope A Conclave Of Contenders
May 12, 2025 -
Key Aaron Judge Analytics Predicting Yankees 2025 Success
May 12, 2025 -
Trumps Budget Director Russ Vought And The Dogecoin Agenda
May 12, 2025 -
Did Sylvester Stallone Regret Rejecting A Role In 1978s Coming Home
May 12, 2025