Improving Automated Visual Inspection Of Lyophilized Vials: A Practical Guide
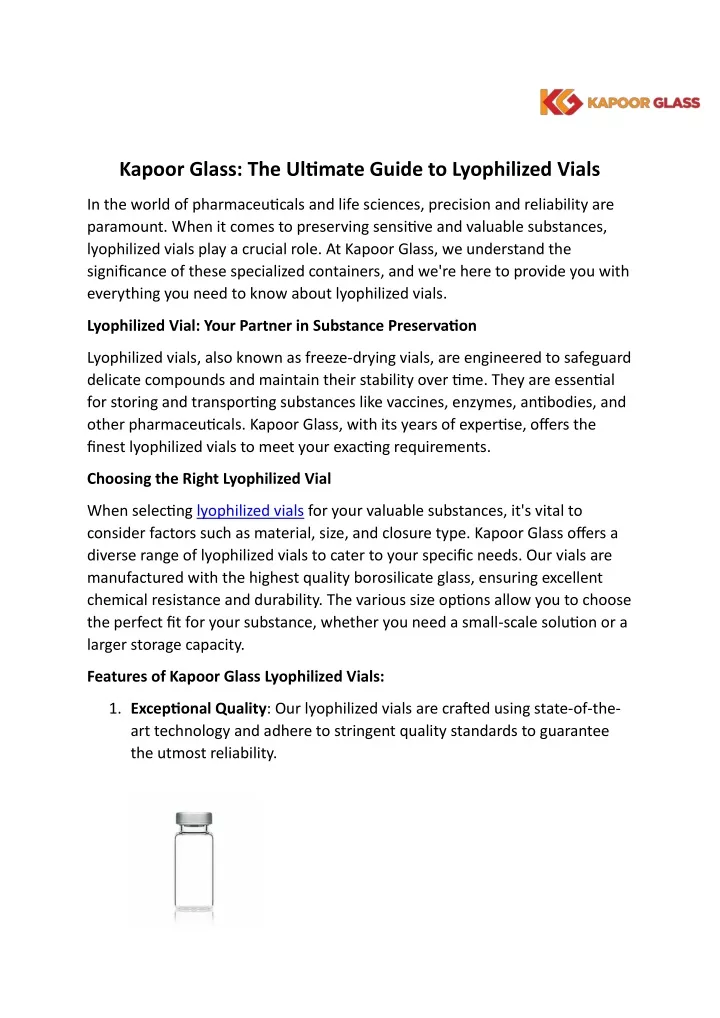
Table of Contents
Selecting the Right Automated Visual Inspection System
Choosing the right automated visual inspection system is paramount for effective quality control. The system's capabilities must align precisely with the specific needs of your lyophilized vial production process.
Understanding System Capabilities
Different technologies underpin automated visual inspection systems, each with strengths and weaknesses. Machine vision systems utilize image processing techniques to analyze images of the vials, identifying defects such as cracks, particulate matter, and fill level discrepancies. Understanding these technologies is crucial for selecting the optimal system.
- Comparison of Imaging Technologies: CCD (Charged Coupled Device) and CMOS (Complementary Metal-Oxide-Semiconductor) sensors are common choices. CCD sensors often offer higher image quality but can be more expensive than CMOS sensors, which are known for their speed and lower cost. The choice depends on your specific needs and budget.
- Resolution Considerations: High-resolution imaging is crucial for detecting subtle defects. The system's resolution should be sufficient to identify even the smallest imperfections, ensuring the highest level of quality control.
- Lighting Techniques: Appropriate lighting is essential for optimal defect detection. Different lighting techniques, such as dark field and bright field illumination, highlight defects differently. Careful consideration of lighting parameters is critical for maximizing the sensitivity of the inspection system.
Keywords: Machine vision, image processing, defect detection, CCD, CMOS, high-resolution imaging, lyophilized vial inspection systems.
Integration with Existing Production Lines
Integrating an automated system into existing workflows requires careful planning and consideration. Seamless integration minimizes disruption and ensures efficient operation.
- System Footprint: The physical size of the system must be compatible with the available space on your production line.
- Equipment Compatibility: The system needs to be compatible with existing equipment such as vial filling machines and conveyor systems.
- Data Management: A robust data management system is essential for storing and retrieving inspection results, ensuring compliance with regulatory requirements. The system should seamlessly integrate with your existing data infrastructure.
- Validation Protocols: Thorough validation according to guidelines like 21 CFR Part 11 is crucial to demonstrate system performance and compliance with Good Manufacturing Practices (GMP).
Keywords: System integration, production line integration, data management, validation, 21 CFR Part 11, GMP compliance.
Optimizing Image Acquisition and Processing
Optimizing image acquisition and processing directly impacts the accuracy and efficiency of defect detection.
Illumination Strategies for Enhanced Defect Visibility
Proper illumination is critical for highlighting defects. Different lighting techniques offer distinct advantages.
- Dark Field Illumination: This technique enhances the visibility of particulate matter and other small defects by illuminating the vial from the sides, creating a dark background against which defects stand out.
- Bright Field Illumination: Suitable for detecting larger defects like cracks or fill level discrepancies, this method illuminates the vial directly.
- Impact on Defect Detection Sensitivity: The choice of illumination method significantly impacts the sensitivity of defect detection. Careful experimentation may be needed to optimize lighting parameters for your specific application.
- Minimizing Shadows and Reflections: Shadows and reflections can mask defects. Careful positioning of the light sources and the use of anti-reflective coatings can help minimize these issues.
Keywords: Lighting techniques, dark field illumination, bright field illumination, contrast enhancement, shadow reduction, image optimization.
Advanced Image Processing Algorithms
Sophisticated algorithms enhance the speed and accuracy of defect detection.
- AI-Powered Defect Classification: Artificial intelligence and machine learning algorithms can learn to classify defects based on training data, leading to improved accuracy and reduced false positives.
- Algorithm Training and Validation: Proper training and validation of the algorithms are crucial to ensure their accuracy and reliability. This often involves using a large dataset of images with known defects.
- Handling Variations in Vial Characteristics: Algorithms must be robust enough to handle variations in vial characteristics, such as slight differences in fill levels or vial geometry, without triggering false alarms.
Keywords: AI, machine learning, image processing algorithms, defect classification, algorithm training, deep learning.
Ensuring Data Integrity and Regulatory Compliance
Maintaining data integrity and regulatory compliance is vital for the pharmaceutical industry.
Data Management and Traceability
Robust data management systems are crucial for traceability and regulatory compliance.
- Data Logging Capabilities: The system should accurately log all inspection results, including timestamps, vial identifiers, and defect details.
- Report Generation: Automated report generation facilitates analysis of inspection data, identifying trends and areas for improvement.
- Audit Trails: Comprehensive audit trails are essential for demonstrating compliance with regulatory requirements, such as 21 CFR Part 11.
- Integration with Other Quality Control Systems: The system should integrate seamlessly with other quality control systems, providing a holistic view of the manufacturing process.
- Data Security: Data security measures should be in place to protect sensitive data from unauthorized access or modification.
Keywords: Data management, data traceability, audit trail, report generation, data security, quality control, regulatory compliance.
Validation and Qualification
Thorough validation and qualification are essential for ensuring the accuracy and reliability of the automated inspection system.
- IQ/OQ/PQ Validation: Installation Qualification (IQ), Operational Qualification (OQ), and Performance Qualification (PQ) are crucial steps to verify that the system is installed, operates, and performs as intended.
- Performance Verification: Regular performance verification tests are necessary to ensure ongoing accuracy and reliability.
- Ongoing Calibration: Regular calibration of the system is essential to maintain its accuracy over time.
- Regulatory Requirements: Compliance with all relevant regulatory requirements is paramount.
Keywords: Validation, qualification, IQ/OQ/PQ, performance verification, calibration, regulatory compliance, GMP.
Conclusion
Implementing automated visual inspection of lyophilized vials offers significant advantages in terms of efficiency, accuracy, and regulatory compliance. By carefully selecting the appropriate system, optimizing image acquisition and processing, and ensuring data integrity, pharmaceutical manufacturers can significantly improve their quality control processes and reduce the risk of product defects. Investing in the right automated visual inspection solution is crucial for maintaining high-quality standards and meeting the ever-increasing demands of the pharmaceutical industry. Explore the latest advancements in automated visual inspection technology to enhance your lyophilized vial production processes.
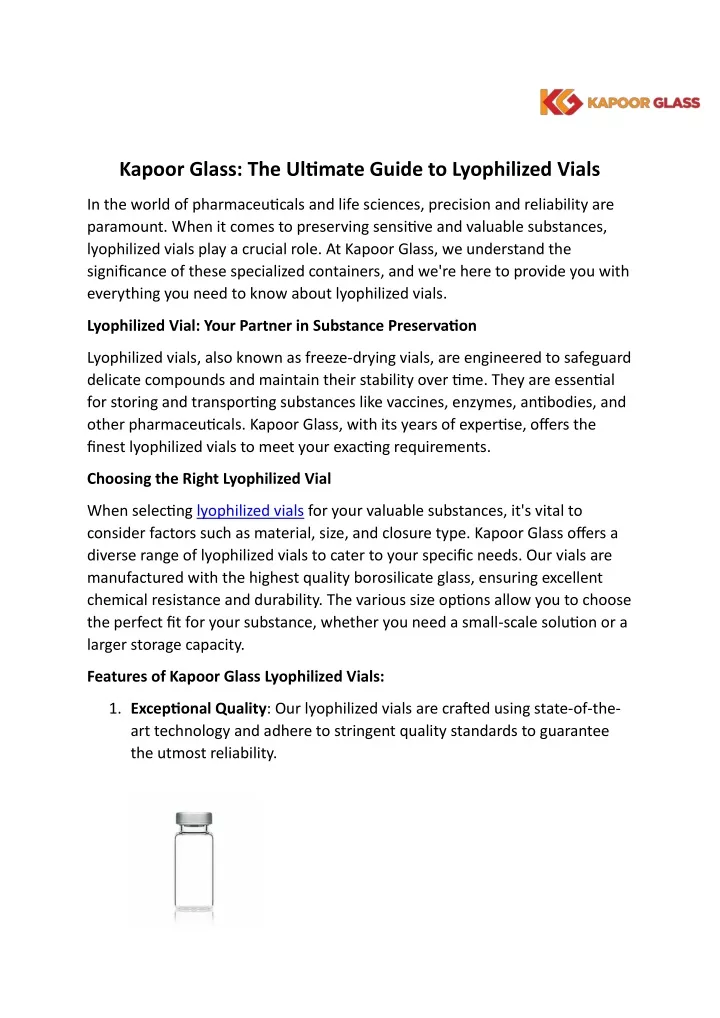
Featured Posts
-
Superyacht Salvage Operation Ends In Divers Death
May 11, 2025 -
Shevchenko Weili Superfight Ufc 315s Potential Showdown
May 11, 2025 -
Exclusive Report Elliotts Strategic Play In Russian Gas Pipeline
May 11, 2025 -
Instagram Ceos Testimony The Fight Against Tik Toks Growth
May 11, 2025 -
2025 Indy 500 Which Driver Wont Be Competing
May 11, 2025