Pentagon Audit Highlights F-35 Inventory Management Failures
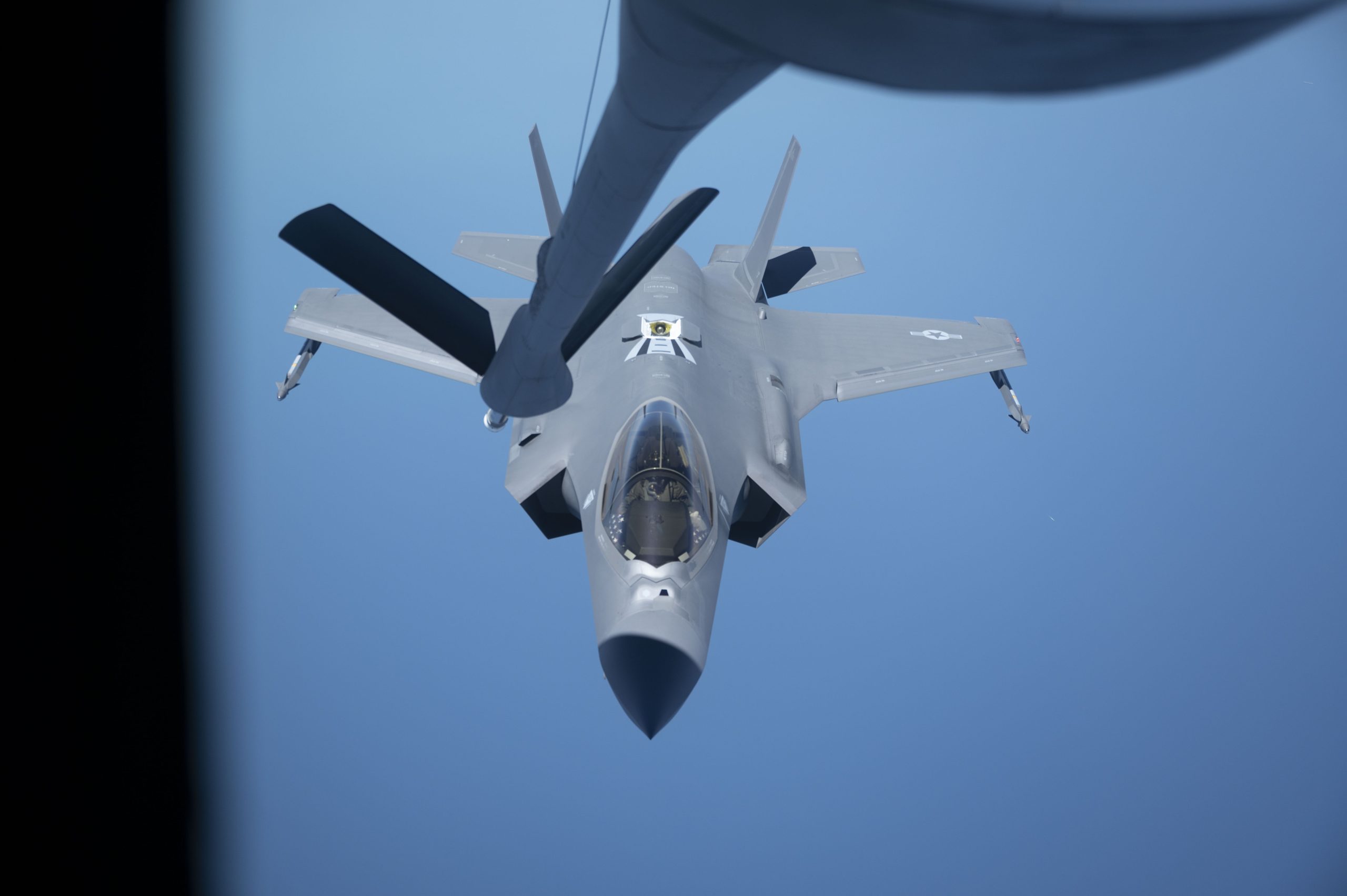
Table of Contents
Significant Discrepancies in F-35 Parts and Component Tracking
The Pentagon audit revealed alarming discrepancies in the tracking of F-35 parts and components. The scale of the problem is vast, impacting the entire supply chain, from initial procurement to maintenance and repair. The audit uncovered instances of missing parts, inaccurate records, and significant logistical bottlenecks that hinder the timely maintenance and repair of the aircraft. These issues are not isolated incidents but rather systemic failures within the F-35 logistics system.
- Lack of real-time inventory tracking systems: The current system relies on outdated and fragmented databases, making it difficult to obtain an accurate picture of available parts. This lack of real-time visibility hampers efficient inventory management and contributes to delays.
- Inefficient data management leading to inaccurate reporting: Data inconsistencies and errors across different databases lead to unreliable inventory reports, making it challenging to accurately assess the availability of crucial components. This further exacerbates the problems associated with F-35 inventory control.
- Problems with part identification and serialization: The lack of standardized part identification and serialization methods complicates tracking and inventory management. This makes it difficult to ensure the correct parts are used for maintenance and repairs.
- Delays in receiving and distributing crucial components: Significant delays in receiving and distributing parts from suppliers and across various maintenance facilities contribute to extended aircraft downtime. This is a major challenge in managing the complex F-35 supply chain.
Impact on F-35 Maintenance and Operational Readiness
The consequences of these F-35 inventory management failures extend far beyond mere record-keeping issues. They directly impact the maintenance schedules, operational readiness, and ultimately, the combat effectiveness of the F-35 fleet.
- Increased aircraft downtime due to missing parts: The inability to quickly obtain necessary parts leads to extended periods of aircraft downtime, reducing the number of aircraft available for deployment.
- Higher maintenance costs stemming from delays and inefficiencies: Delays in maintenance caused by parts shortages result in increased labor costs and expenses associated with expedited shipping and procurement.
- Reduced mission capability and combat effectiveness: A reduction in the number of operational aircraft directly translates to a diminished mission capability and potentially compromises combat effectiveness.
- Potential safety risks associated with inadequate maintenance: Delays in maintenance due to parts shortages could potentially compromise the safety and airworthiness of the F-35 aircraft.
Cost Overruns Exacerbated by Poor F-35 Inventory Management
The financial implications of these inventory management issues are staggering, adding to the already exorbitant cost of the F-35 program. Poor management practices result in significant cost overruns across various aspects of the program.
- Increased procurement costs due to expedited orders for missing parts: The need to expedite orders for missing parts significantly increases procurement costs, as suppliers often charge premiums for faster delivery.
- Higher storage and logistics expenses due to inefficient processes: Inefficient inventory management leads to increased storage costs for excess parts and higher logistics expenses associated with moving parts between locations.
- Wasted resources due to obsolete or misplaced parts: Poor tracking and management can result in parts becoming obsolete or misplaced, leading to wasted resources and unnecessary expenses.
- Potential for fraud and waste due to lack of oversight: The lack of proper oversight and accountability mechanisms increases the risk of fraud and waste within the F-35 logistics system.
Recommendations for Improving F-35 Inventory Management
The Pentagon audit concludes with several crucial recommendations for improving the F-35 inventory management system. These recommendations are critical to ensuring the long-term operational readiness and cost-effectiveness of the program.
- Investment in modern, integrated inventory management software: Implementing a real-time, integrated inventory management system is paramount for tracking parts and ensuring accurate reporting.
- Improved data management practices and standardization across the supply chain: Improved data standardization and integration across the entire supply chain will streamline processes and enhance accuracy.
- Enhanced tracking and tracing of parts using RFID or blockchain technology: Implementing advanced tracking technologies such as RFID or blockchain can provide greater visibility and security in managing the F-35 supply chain.
- Strengthened oversight and accountability mechanisms to prevent future failures: Establishing robust oversight and accountability mechanisms will help to prevent future failures and ensure the effective implementation of recommended improvements.
Conclusion: Addressing F-35 Inventory Management Challenges for a More Efficient and Effective Air Force
The Pentagon audit’s findings regarding F-35 inventory management failures are alarming, highlighting significant consequences for cost, readiness, and safety. The sheer scale of the issues demands immediate and decisive action. Addressing these challenges through the implementation of the recommended improvements—including investment in modern technology, improved data management, and enhanced oversight—is crucial for ensuring the long-term success and effectiveness of the F-35 program. We urge readers to stay informed about the ongoing efforts to improve F-35 logistics, advocate for better F-35 supply chain management, and demand enhanced F-35 inventory control to ensure the successful deployment and operational readiness of this vital asset for our Air Force.
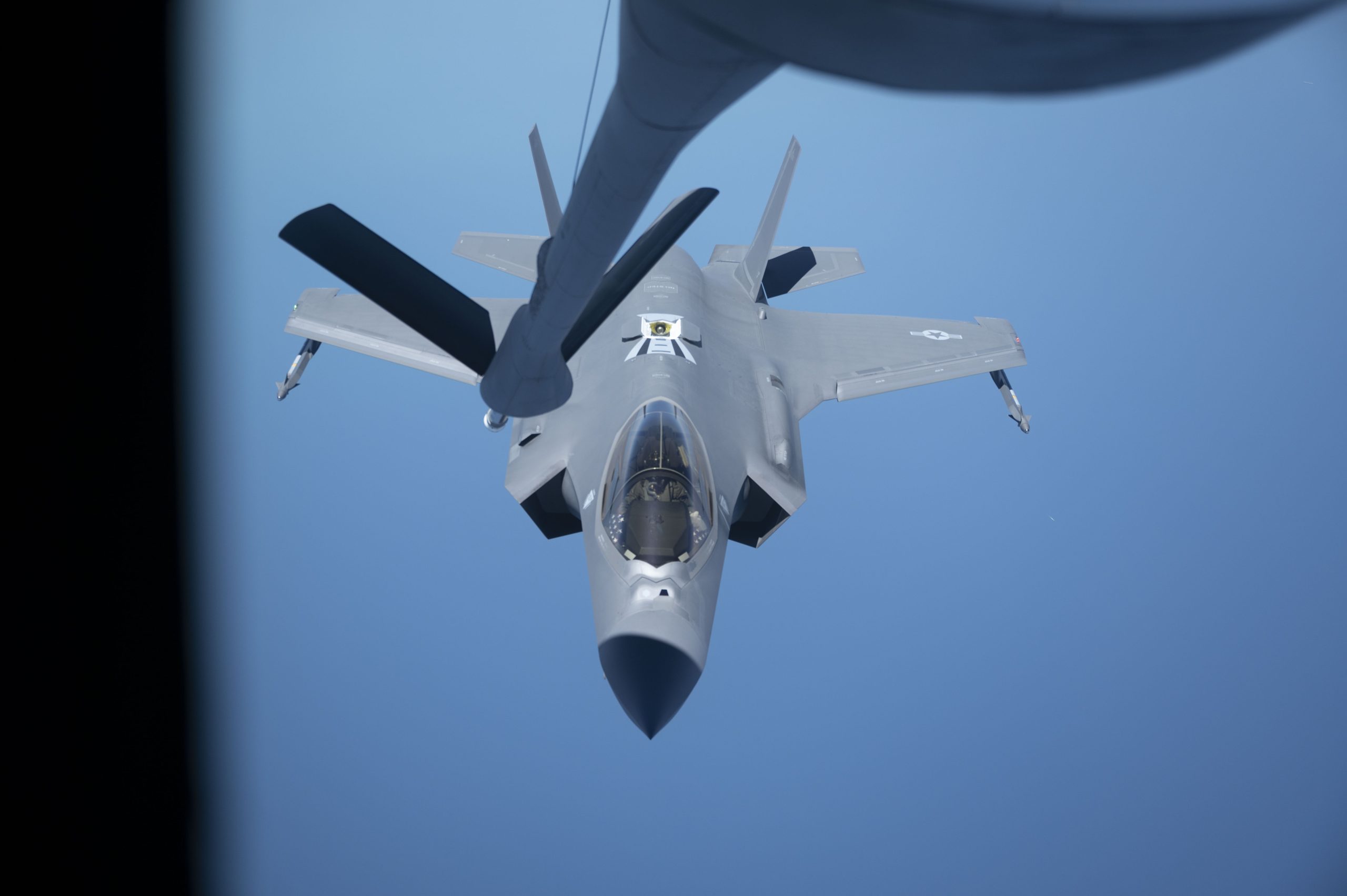
Featured Posts
-
Akhbar Srf Rwatb Abryl 2025 Melwmat Hamt L 13 Mlywn Mwatn
Apr 30, 2025 -
Saltillo Y La Jornada Nacional El Poder Transformador Del Boxeo
Apr 30, 2025 -
Update On Louisville Mail Delivery Delays
Apr 30, 2025 -
Geen Aanklacht Tegen Beyonce En Jay Z In Diddy Zaak
Apr 30, 2025 -
Outdated Software The Hidden Enemy Of Your Ai Strategy
Apr 30, 2025