U.S. Businesses Implement Cost-Cutting Strategies In Response To Tariffs
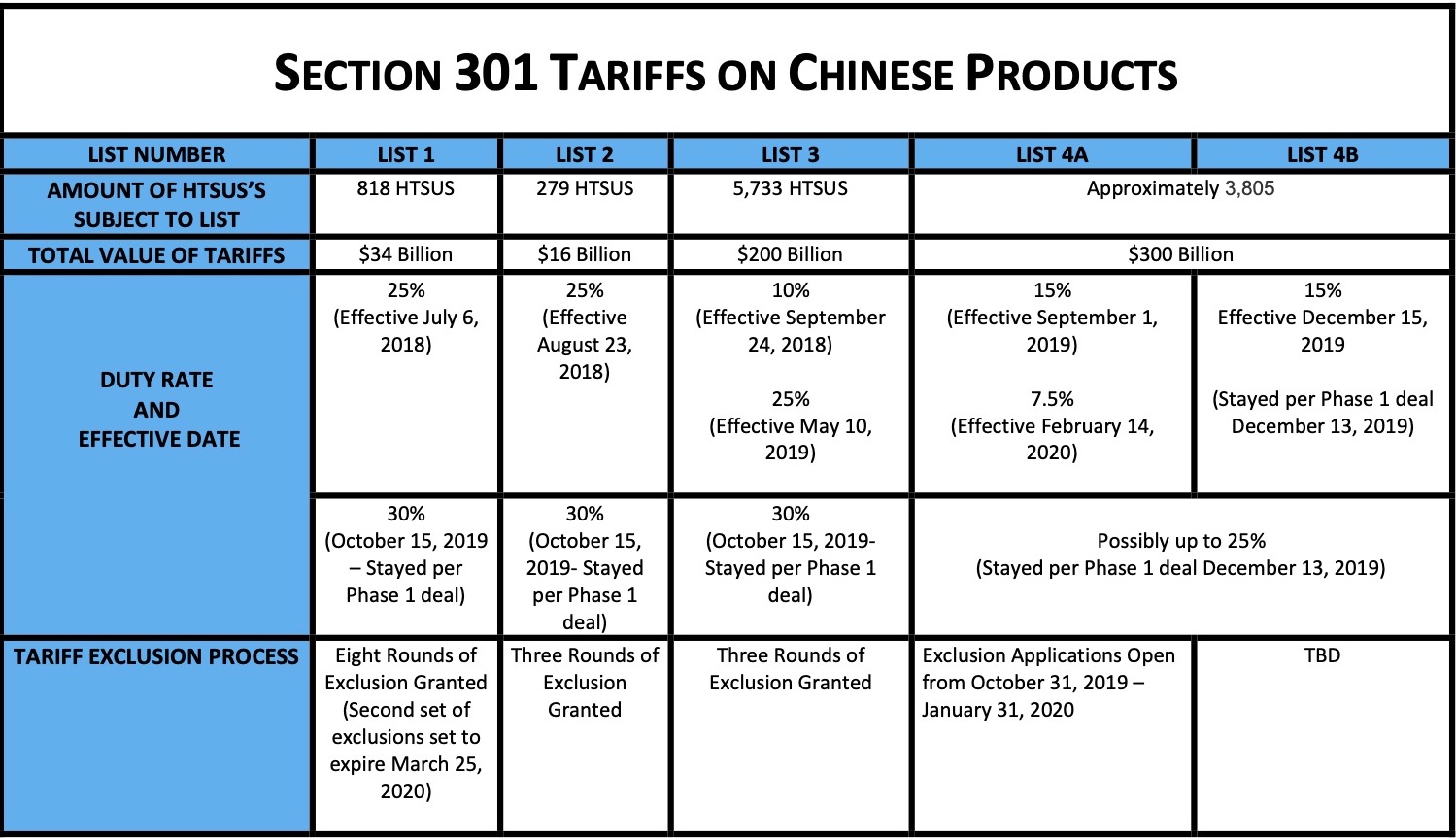
Table of Contents
The imposition of tariffs has significantly impacted U.S. businesses, creating a challenging economic landscape. To maintain profitability and competitiveness, companies across various sectors are implementing creative cost-cutting strategies. This article delves into the diverse approaches businesses are taking to navigate these economic headwinds, exploring effective methods and their implications for the future of American business. We'll examine how companies are adapting to tariffs and what steps they're taking to not just survive, but thrive.
Restructuring Supply Chains to Minimize Tariff Impact
The impact of tariffs on imported goods has forced many businesses to rethink their supply chains. Strategies focused on reducing reliance on high-tariff regions are becoming increasingly crucial for maintaining competitiveness.
Nearshoring and Reshoring: Bringing Production Closer to Home
Many companies are actively pursuing near-shoring (moving production to nearby countries) and reshoring (returning production to the U.S.) to circumvent tariffs. This shift, while offering benefits, presents challenges:
- Increased domestic manufacturing jobs: This is a significant positive, boosting local economies and reducing reliance on foreign labor.
- Higher transportation costs: Shipping goods shorter distances might seem cheaper, but overall transportation costs can fluctuate and may not always be lower than before.
- Potential challenges in finding skilled labor: The availability of a skilled workforce in the U.S. can vary significantly by region and industry, requiring investment in training and development.
Example: A clothing manufacturer previously based in China is relocating its production to Mexico to leverage lower labor costs and avoid significant U.S. tariffs on Chinese imports.
Diversifying Sourcing: Reducing Reliance on Single Suppliers
Another key strategy is diversifying sourcing. Instead of relying on a single supplier, companies are spreading their sourcing across multiple countries and suppliers. This mitigates the risk associated with tariffs imposed on goods from a single nation. However, diversification introduces new complexities:
- Increased supplier management complexity: Managing multiple suppliers requires more robust systems and processes.
- Potential quality control challenges: Maintaining consistent quality across different suppliers can be difficult.
- Negotiating better terms with multiple suppliers: This requires strong negotiation skills and potentially more administrative work.
Example: A technology company that previously sourced all its components from China is now sourcing them from multiple countries like Vietnam, Taiwan, and Mexico, to mitigate tariff risks.
Negotiating Better Trade Deals with Suppliers: Sharing the Burden
Companies are actively negotiating with existing suppliers to share the burden of tariffs. This may involve renegotiating contracts to secure more favorable pricing and terms. While this approach can be effective, it is not without its potential downsides:
- Requires strong negotiating skills: Effective negotiation is crucial to reach mutually beneficial agreements.
- Potential for strained supplier relationships: Aggressive negotiation can strain relationships with suppliers if not handled carefully.
- Increased administrative burden: Renegotiating contracts involves significant administrative overhead.
Example: A furniture importer is renegotiating contracts with its suppliers in order to absorb a portion of the tariff increase, reducing the impact on their final pricing.
Optimizing Internal Operations for Cost Savings
Beyond supply chain restructuring, U.S. businesses are also focusing on internal operational efficiencies to reduce costs.
Automation and Technology Adoption: Increasing Efficiency
Automation and technology adoption are crucial for reducing labor costs and increasing productivity in the face of rising tariffs. While this approach offers significant long-term benefits, it also requires substantial upfront investment:
- High upfront investment costs: Implementing automation often requires significant initial capital expenditure.
- Potential job displacement: Automation can lead to job losses in some sectors, although it can also create new jobs in other areas.
- Long-term cost savings through increased productivity: The eventual return on investment can be substantial, leading to substantial long-term cost savings.
Example: A factory is implementing robotic assembly lines to increase production efficiency and reduce labor costs associated with manual assembly.
Lean Manufacturing Principles: Eliminating Waste and Improving Efficiency
Lean manufacturing principles, focusing on eliminating waste and optimizing processes, are becoming increasingly important for cost reduction. This requires a commitment to ongoing improvement and employee training:
- Requires employee training: Implementing lean manufacturing requires employees to be trained in new methods and processes.
- Careful process mapping: Identifying and eliminating waste requires careful mapping and analysis of existing processes.
- Potential for increased productivity and reduced waste: Successfully implemented lean manufacturing leads to significant improvements in productivity and a reduction in waste.
Example: A food processing plant is implementing Kaizen methods (continuous improvement) to streamline its production processes and reduce waste.
Inventory Management Strategies: Optimizing Stock Levels
Effective inventory management is crucial for minimizing storage costs and preventing waste. Sophisticated inventory management systems are key to success, but they require careful planning and implementation:
- Requires sophisticated inventory management systems: Implementing Just-in-Time or similar inventory management strategies requires sophisticated systems and processes.
- Risk of stockouts: Poorly implemented inventory management can lead to stockouts, affecting production and sales.
- Potential for significant cost savings: Effective inventory management can lead to significant savings in storage and waste reduction.
Example: A retailer is implementing Just-in-Time (JIT) inventory management to minimize storage costs and reduce the risk of obsolescence.
Government Support and Policy Responses: Seeking External Assistance
U.S. businesses can also leverage government support programs and policies to mitigate the impact of tariffs.
Tariff Relief Programs: Navigating Government Assistance
Various government programs offer tariff relief or exclusions for specific industries. However, accessing these programs can be complex:
- Eligibility requirements: These programs often have specific eligibility requirements that businesses must meet.
- Application processes: The application process for these programs can be time-consuming and complicated.
- Potential financial assistance: Successful applicants may receive financial assistance to offset the impact of tariffs.
Example: A small business applies for a tariff exclusion for a specific product to reduce its import costs.
Tax Incentives and Subsidies: Leveraging Government Support
Federal and state governments offer various tax incentives and subsidies to support businesses and encourage investment. Understanding these programs is critical for cost reduction:
- Specific eligibility criteria: Tax incentives and subsidies often have specific eligibility criteria.
- Application processes: Accessing these incentives requires navigating specific application processes.
- Limitations and potential benefits: While beneficial, these programs may have limitations and specific requirements.
Example: A manufacturer benefits from tax credits for investing in new equipment that improves efficiency and reduces reliance on imported parts.
Conclusion
The imposition of tariffs has presented significant challenges for U.S. businesses, forcing them to adopt proactive and innovative cost-cutting strategies. By strategically restructuring their supply chains, optimizing internal operations, and actively seeking government support, companies can effectively navigate these difficulties and maintain profitability. These strategies not only mitigate the negative impacts of tariffs but also foster long-term growth and competitiveness in a globalized marketplace. Don't wait for tariffs to cripple your business; proactively implement effective cost-cutting strategies and ensure your continued success in the face of ongoing trade complexities. Start exploring your options for mitigating the impact of U.S. tariffs today.
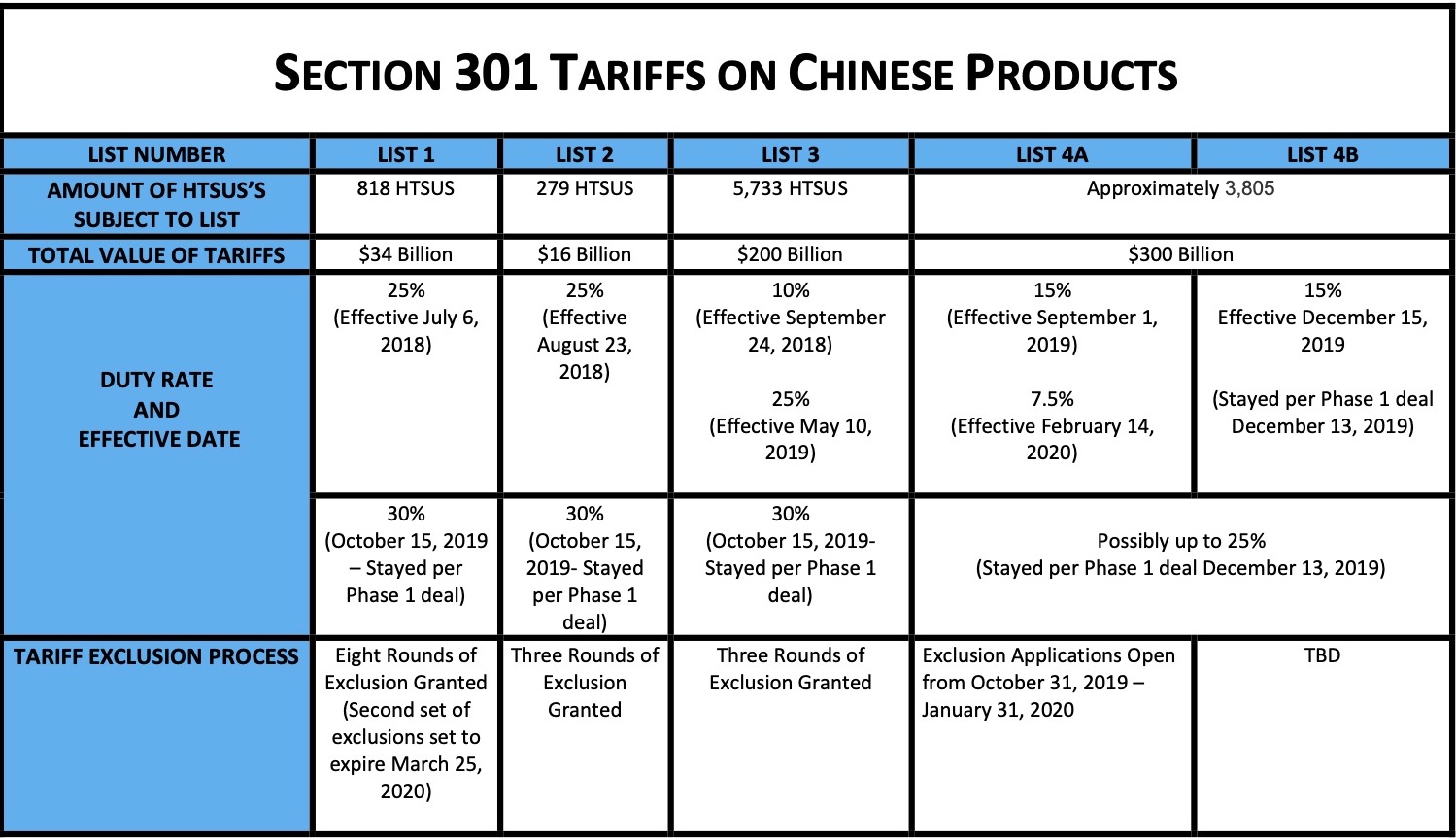
Featured Posts
-
Germanys Stricter Border Controls Lowest Migration Since Covid 19
Apr 29, 2025 -
Understanding The Tik Tok Adhd Connection Fact Vs Fiction
Apr 29, 2025 -
2025 Porsche Cayenne Interior And Exterior Photo Gallery
Apr 29, 2025 -
Iva Sofiyanska Izplyu Kamcheto I Zascho Ya Uvolnikha Ot Televiziyata
Apr 29, 2025 -
Capital Summertime Ball 2025 Tickets Your Guide To Purchase
Apr 29, 2025