Week In Review: Analyzing Past Failures For Future Success
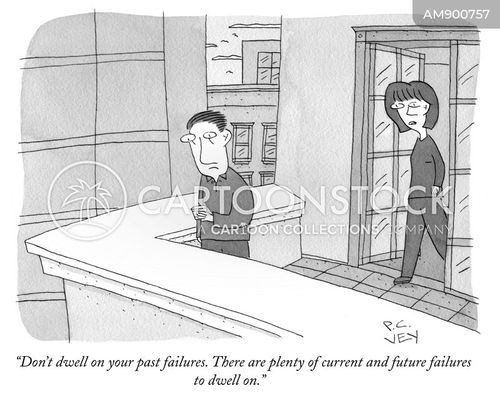
Table of Contents
Identifying Key Failures
Before we can learn from our mistakes, we must first identify them. This involves a crucial step: defining what constitutes a "failure."
Defining "Failure":
It's essential to distinguish between genuine failures and minor setbacks. Objectivity is key here. A "failure" is a significant deviation from a planned outcome, resulting in a negative impact. A "learning opportunity," on the other hand, is a less severe setback that provides valuable insights without causing significant damage.
- Examples of Failures: Missed deadlines leading to project delays, flawed product launches resulting in customer dissatisfaction, or missed sales targets impacting revenue.
- Examples of Learning Opportunities: Minor bugs in software requiring a quick fix, a slightly delayed email response, or a misinterpreted client request clarified through communication.
- Process Failures vs. Outcome Failures: A process failure is a flaw in the system or methodology, while an outcome failure is the negative result of a flawed process. Identifying both is crucial for effective failure analysis.
To identify significant failures, use this simple checklist:
- Did the event significantly impact your goals?
- Did it cause unexpected costs or delays?
- Did it damage your reputation or relationships?
- Does it warrant a deeper investigation?
Documenting Failures:
Detailed record-keeping is crucial for effective failure analysis. Without documentation, lessons learned are easily forgotten.
- Methods for Documentation: Maintain a dedicated journal, utilize project management software (like Asana or Trello) to track issues, or keep detailed meeting notes focusing on what went wrong.
- Templates and Frameworks: Consider using a standardized template to document failures, including a description of the event, the impact, potential causes, and corrective actions. This ensures consistency and facilitates future analysis.
- Consistent Format: A consistent format for documenting failures streamlines the process and enables easier identification of patterns and trends over time.
Root Cause Analysis
Once failures are identified and documented, we can move on to root cause analysis – uncovering the underlying issues that contributed to the failure.
Uncovering the Underlying Issues:
Several techniques can help uncover the root cause. Two popular methods are:
- The "5 Whys": Repeatedly ask "why" to peel back the layers of the problem and get to the core issue. For example: "The project was late (Why?) because we underestimated the task. (Why?) Because we lacked accurate data. (Why?) Because our data collection process was flawed. (Why?) Because we didn't have the right tools. (Why?) Because management didn't prioritize resource allocation."
- Fishbone Diagrams (Ishikawa Diagrams): A visual tool that helps identify all potential contributing factors categorized by category (e.g., methods, materials, manpower, machines, measurements, environment).
Step-by-step guide for conducting root cause analysis:
- Clearly define the problem.
- Gather relevant data and information.
- Apply a chosen root cause analysis technique.
- Identify the root cause(s).
- Verify the root cause(s).
It's critical to avoid assigning blame during this phase. The goal is to identify systemic issues, not individual shortcomings.
Identifying Contributing Factors:
Distinguishing between primary and secondary causes is crucial. The primary cause is the most significant factor directly leading to the failure, while secondary causes are contributing factors that exacerbated the issue.
Common Contributing Factors:
Factor | Potential Solutions |
---|---|
Lack of resources | Improved budgeting, resource allocation, and prioritization |
Insufficient training | Comprehensive training programs, mentorship opportunities |
Poor communication | Improved communication protocols, regular team meetings |
Inadequate planning | More thorough planning processes, risk assessments |
Technological issues | Regular system maintenance, robust backup systems |
External factors (e.g., market changes) | Adaptable strategies, contingency planning |
Consider both internal and external factors when conducting your analysis.
Developing Actionable Strategies
The final, and perhaps most important, step is transforming the findings of your failure analysis into actionable strategies for improvement.
Formulating Corrective Actions:
Translate your root cause analysis into specific, measurable, achievable, relevant, and time-bound (SMART) goals.
- Examples of Corrective Actions: Implementing a new project management system, developing a more robust training program, improving communication protocols, or allocating additional resources to critical tasks.
- Accountability and Monitoring: Assign responsibility for implementing corrective actions and establish a system for monitoring progress and ensuring accountability.
Preventing Future Failures:
Focus on proactive measures to prevent similar issues from recurring.
- Preventative Measures: Implementing regular quality control checks, conducting thorough risk assessments, establishing clear communication protocols, and creating a culture of continuous improvement.
- Risk Management Tools: Utilize tools like SWOT analysis, risk registers, and probability/impact matrices to proactively identify and mitigate potential risks.
- Continuous Improvement: Embrace a culture of continuous learning and improvement, regularly reviewing processes and seeking feedback to prevent future failures.
Conclusion
By consistently analyzing past failures, you gain valuable insights into your processes, identify weaknesses, and develop strategies for future success. This "Week in Review" process, focusing on analyzing past failures, allows you to transform setbacks into stepping stones. Remember the key takeaways: identifying failures, conducting thorough root cause analysis, and formulating actionable strategies to prevent future occurrences. Start analyzing past failures today to unlock your potential for success. Implement a weekly failure analysis process to achieve significant improvements. By consistently analyzing past failures, you will pave the way for remarkable success.
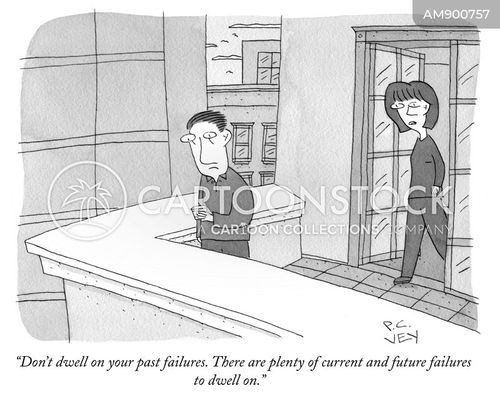
Featured Posts
-
Bajerna Arena Domacin Generalne Probe Srbije Pred Evrobasket
May 17, 2025 -
Ahorra En La Fiesta Del Cine 2025 Entradas A 3000 Y Programacion
May 17, 2025 -
Lietuvos Krepsinio Rinktines Sudetyje Wnba Zaideja J Jocyte
May 17, 2025 -
Investing In Growth Identifying The Countrys Emerging Business Centers
May 17, 2025 -
Referee Controversy Thibodeaus Reaction To Knicks Game 2 Loss
May 17, 2025