The Future Of Automated Visual Inspection For Lyophilized Vials: Addressing Current Limitations
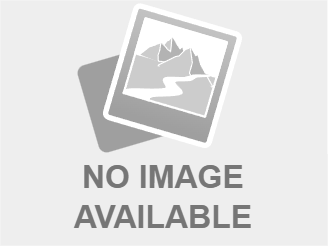
Table of Contents
Current Limitations of Automated Visual Inspection for Lyophilized Vials
Current automated visual inspection systems for lyophilized vials, while valuable, still present significant hurdles in achieving perfect quality control. These limitations impact efficiency, accuracy, and ultimately, patient safety.
Challenges in Detecting Subtle Defects
Many defects in lyophilized vials are incredibly subtle and difficult to detect with current AVI technology. These include: hairline cracks in the glass, microscopic particulate matter within the vial, inconsistencies in the fill level of the lyophilized product, and variations in the appearance of the lyophilized cake. Such seemingly minor defects can compromise product quality and patient safety, leading to potential recalls and significant financial losses. Advanced image processing algorithms are desperately needed to improve the sensitivity of defect detection.
- Difficulties with transparent vial detection: The transparency of the glass can make it challenging to detect internal defects.
- Variations in lighting and vial orientation: Inconsistent lighting or the angle at which the vial is presented can obscure defects.
- Issues with differentiating between defects and harmless variations: Distinguishing between actual defects and normal variations in the lyophilization process can be difficult for current systems, leading to false positives.
High False-Positive Rates
A major drawback of many current AVI systems is their high false-positive rate. This means the system frequently flags vials as defective when they are, in fact, perfectly acceptable. This leads to increased inspection times, unnecessary rejection of good products, wasted resources, and ultimately, increased production costs. Improved machine learning algorithms are crucial to mitigate this problem and enhance the accuracy of defect detection. This requires extensive training data sets featuring images of both defective and non-defective vials, allowing the AI to learn the subtle differences and improve its classification accuracy.
- Implementation of advanced image filtering techniques: These can help to remove noise and enhance the contrast of defects.
- Use of AI and machine learning for improved defect classification: AI and ML can learn to recognize subtle patterns indicative of defects that are missed by traditional algorithms.
- Development of more robust and adaptable algorithms: Algorithms that can adapt to variations in lighting, vial orientation, and other factors will improve the accuracy and reduce false positives.
Limitations in Throughput and Speed
The speed at which current AVI systems can inspect lyophilized vials often fails to meet the demands of high-volume pharmaceutical production. This limitation creates bottlenecks in the manufacturing process, leading to delays and increased costs. Faster inspection speeds are crucial to improve efficiency and reduce production downtime. Advancements in hardware, software, and image processing are key to achieving this.
- Parallel processing and multi-camera systems: Using multiple cameras and processors simultaneously can significantly speed up the inspection process.
- Optimized imaging algorithms for faster analysis: Developing more efficient algorithms that require less processing time is crucial for increased throughput.
- High-speed robotic handling systems: Automating the handling and positioning of vials using advanced robotics can further accelerate the inspection process.
Technological Advancements Driving the Future of Automated Visual Inspection
The future of automated visual inspection for lyophilized vials is bright, fueled by significant advancements in several key areas.
Artificial Intelligence (AI) and Machine Learning (ML)
AI and ML are transforming automated visual inspection. These technologies offer the potential to significantly improve the accuracy and efficiency of defect detection in lyophilized vials. By training AI algorithms on vast datasets of images, the systems can learn to identify subtle defects that are often missed by traditional methods. This leads to a reduction in both false positives and false negatives, resulting in higher accuracy and improved quality control.
- Examples: Deep learning networks for image classification and convolutional neural networks (CNNs) for defect detection are already being implemented and continually improved.
Advanced Imaging Techniques
Beyond traditional 2D imaging, advanced techniques like hyperspectral imaging and 3D imaging are emerging as powerful tools for automated visual inspection. Hyperspectral imaging captures images across a wide range of wavelengths, providing much richer data about the vial and its contents. 3D imaging creates a three-dimensional model of the vial, allowing for the detection of defects that might be missed by traditional 2D methods.
- Benefits: Enhanced sensitivity, better differentiation of defects, and improved overall accuracy.
Improved Hardware and Robotics
Advancements in hardware are equally important. Faster cameras, more sophisticated lighting systems, and advanced robotic handling systems will all contribute to faster and more efficient inspection processes. This allows for the inspection of a greater number of vials in a shorter time frame, significantly improving overall throughput and reducing costs.
- Integration of advanced robotics: Automated vial handling and positioning improve efficiency and reduce the risk of human error.
Regulatory Considerations and Validation
Meeting regulatory requirements is paramount for any automated visual inspection system used in pharmaceutical manufacturing. Stringent validation protocols are essential to demonstrate the accuracy and reliability of the system, ensuring the safety and quality of the lyophilized products. Thorough documentation is necessary to comply with regulatory guidelines set by agencies like the FDA and EMA.
Conclusion
The future of automated visual inspection for lyophilized vials depends on overcoming current limitations through technological innovation. AI, advanced imaging techniques, and improved hardware are pivotal to enhancing accuracy, speed, and throughput. Meeting regulatory requirements and rigorous validation remain crucial. By embracing these advancements, the pharmaceutical industry can guarantee the consistent quality and safety of lyophilized products, benefiting patients and boosting manufacturing efficiency. Investing in advanced automated visual inspection solutions is not merely an option; it's essential for the future of lyophilized vial manufacturing. Embrace the future of automated visual inspection and elevate your lyophilized vial quality control today!
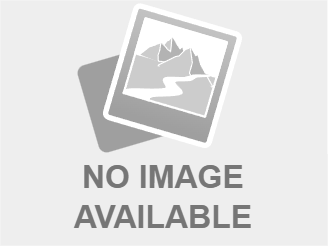
Featured Posts
-
Nba Playoffs 2024 Zeygaria Imerominies And Prognostika
May 11, 2025 -
Nine Contenders Potential Successors To Pope Francis
May 11, 2025 -
Hotel Transylvania A Complete Guide To The Monster Filled Franchise
May 11, 2025 -
Houston Hosts Astros Foundation College Classic What To Expect
May 11, 2025 -
The Power Of Simplicity A Profitable Dividend Investing Approach
May 11, 2025