The Robotic Manufacturing Hurdles In Nike Sneaker Production
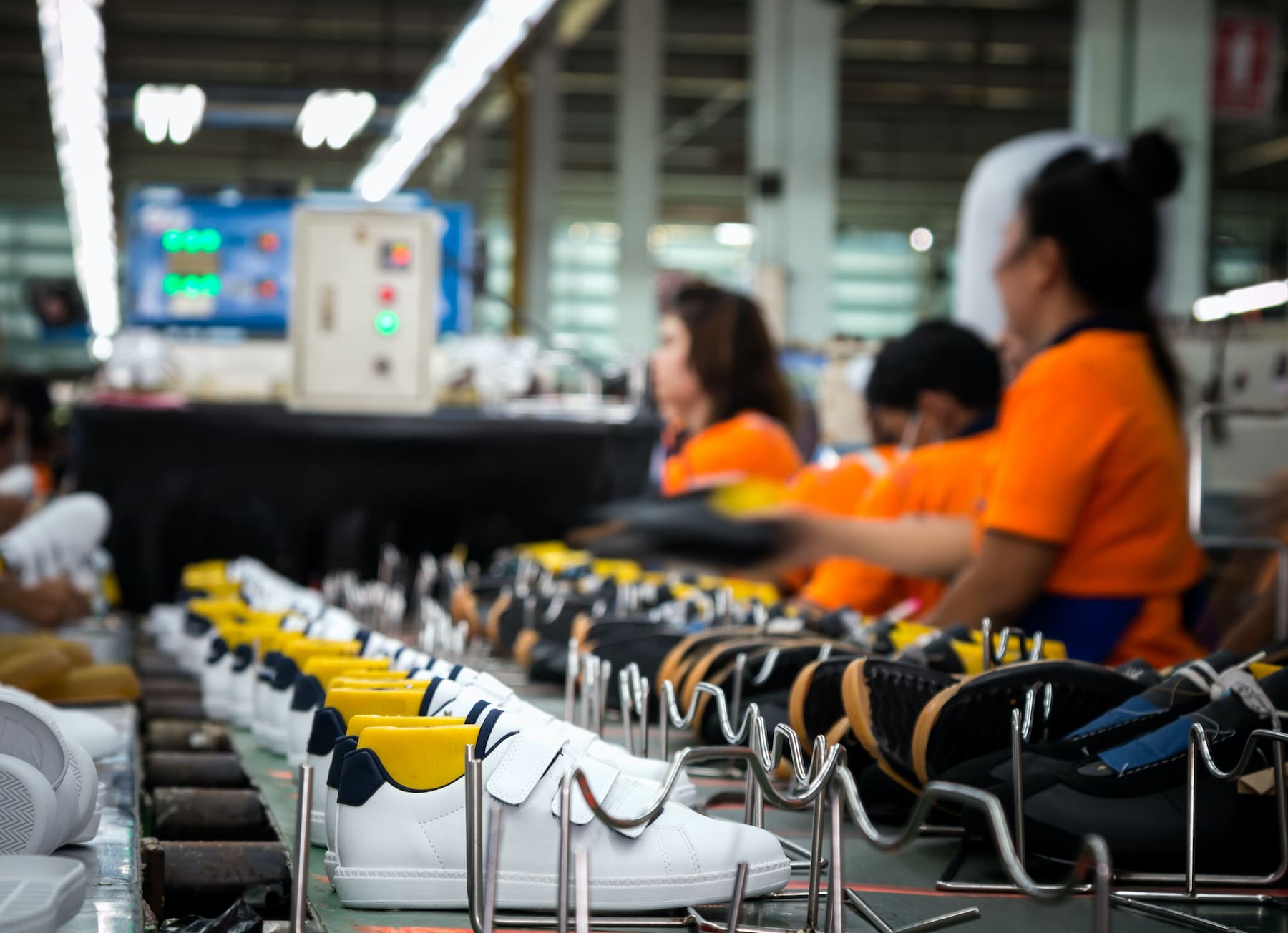
Table of Contents
High Initial Investment Costs and ROI Uncertainty
The high cost of implementing robotic manufacturing is a major barrier for even a company as large as Nike. The initial capital expenditure required to purchase and install advanced robotic systems is substantial. This includes not only the robots themselves but also the necessary supporting infrastructure, such as specialized tooling, conveyor systems, and sophisticated software.
- High upfront costs: Purchasing and integrating advanced robotic arms, vision systems, and control software represents a significant financial commitment.
- Complex ROI calculations: Accurately predicting the return on investment (ROI) for robotic manufacturing is challenging. Factors such as production volume, defect rates, and maintenance costs all influence the overall profitability. A thorough cost analysis, considering both short-term and long-term expenses, is crucial before making such a large investment.
- Specialized infrastructure: Integrating robotics often requires significant modifications to existing factory layouts and infrastructure, adding further to the overall cost. This might involve redesigning production lines, installing new power supplies, and implementing safety systems.
- Skilled technicians: Operating and maintaining robotic systems requires specialized technicians, increasing labor costs and the need for comprehensive training programs.
Technological Limitations and Dexterity Challenges
While robotic automation excels in repetitive, high-precision tasks, sneaker manufacturing involves numerous intricate processes requiring dexterity and adaptability. Current robotic systems struggle with the nuanced movements required for certain aspects of sneaker assembly.
- Intricate tasks: Tasks such as stitching, gluing, and the precise placement of components demand a level of dexterity that many current robots lack. The delicate nature of the materials used in sneaker production also increases the risk of damage during automated processes.
- Complex designs: Nike's diverse range of sneaker models, each with unique designs and materials, presents a challenge for robotic programming. Adapting robotic systems to handle this variability requires significant flexibility and reprogramming.
- Precision and dexterity limitations: Achieving the necessary precision for fine motor skills remains a significant technological hurdle. Current robotic systems often lack the sensitivity and adaptability required for these tasks.
- AI and machine learning advancements: AI and machine learning offer promising avenues for improving robotic dexterity and adaptability. However, these technologies are still under development and require further refinement before widespread implementation in sneaker production.
Adaptability to Diverse Sneaker Models and Styles
Nike's vast range of sneaker models and styles poses a significant challenge for robotic manufacturing. The flexibility required to adapt to different designs, materials, and components necessitates a high degree of adaptability in the robotic systems.
- Customization challenges: Mass customization is a growing trend in the footwear industry, but adapting robotic systems to handle variations in design and materials adds significant complexity and expense.
- Reprogramming costs: The cost of retooling and reprogramming robots for each new sneaker design can quickly negate the cost savings associated with automation.
- Flexible manufacturing systems: The need for flexible manufacturing systems capable of handling diverse product variations is paramount for successful robotic integration.
Job Displacement and Labor Relations
The introduction of robotic manufacturing inevitably raises concerns about job displacement for factory workers. Addressing this challenge requires proactive strategies to minimize negative social impacts.
- Workforce transition: Implementing effective workforce transition strategies, including retraining programs and alternative employment opportunities, is crucial to mitigate job losses and ensure a smooth transition for affected employees.
- Retraining initiatives: Investing in comprehensive retraining programs to equip workers with the skills needed for new roles in the automated manufacturing environment is vital. This might include training in robotics maintenance, programming, or other related fields.
- Labor relations: Maintaining positive labor relations during the transition to robotic manufacturing requires open communication and collaboration between Nike, its employees, and labor unions. Addressing concerns and establishing trust is paramount for a successful implementation.
Supply Chain Integration and Logistics
Integrating robotic systems into Nike's existing supply chain requires careful planning and coordination. Automated material handling and efficient warehouse management systems are essential to support the seamless flow of materials through the production process.
- Supply chain optimization: Seamless integration of robotic systems into existing supply chains requires careful planning and coordination across all stages of the process, from raw material sourcing to finished product distribution.
- Automated material handling: Implementing automated material handling systems, including automated guided vehicles (AGVs) and robotic arms, is crucial for efficient material flow within the manufacturing facility.
- Warehouse automation: Integrating robotic systems into warehouse operations, including automated picking and packing systems, is essential to streamline logistics and reduce storage costs.
- Disruption mitigation: Potential disruptions to the supply chain caused by robotic system malfunctions must be addressed proactively through redundancy planning and robust maintenance protocols.
Conclusion
While robotic manufacturing presents significant opportunities for Nike to enhance efficiency and reduce costs in its sneaker production, several substantial hurdles remain. High initial investment costs, technological limitations, the challenge of adapting to diverse product lines, potential job displacement, and complex supply chain integration all necessitate careful consideration. Overcoming these obstacles requires a comprehensive strategy that combines technological innovation, responsible workforce planning, and proactive management of social and economic impacts. Continued investment in research and development of advanced robotic systems, particularly those incorporating AI and machine learning capabilities, is crucial for unlocking the full potential of robotic manufacturing in the footwear industry. Investing wisely in robotic manufacturing solutions is key to Nike's continued success and global competitiveness.
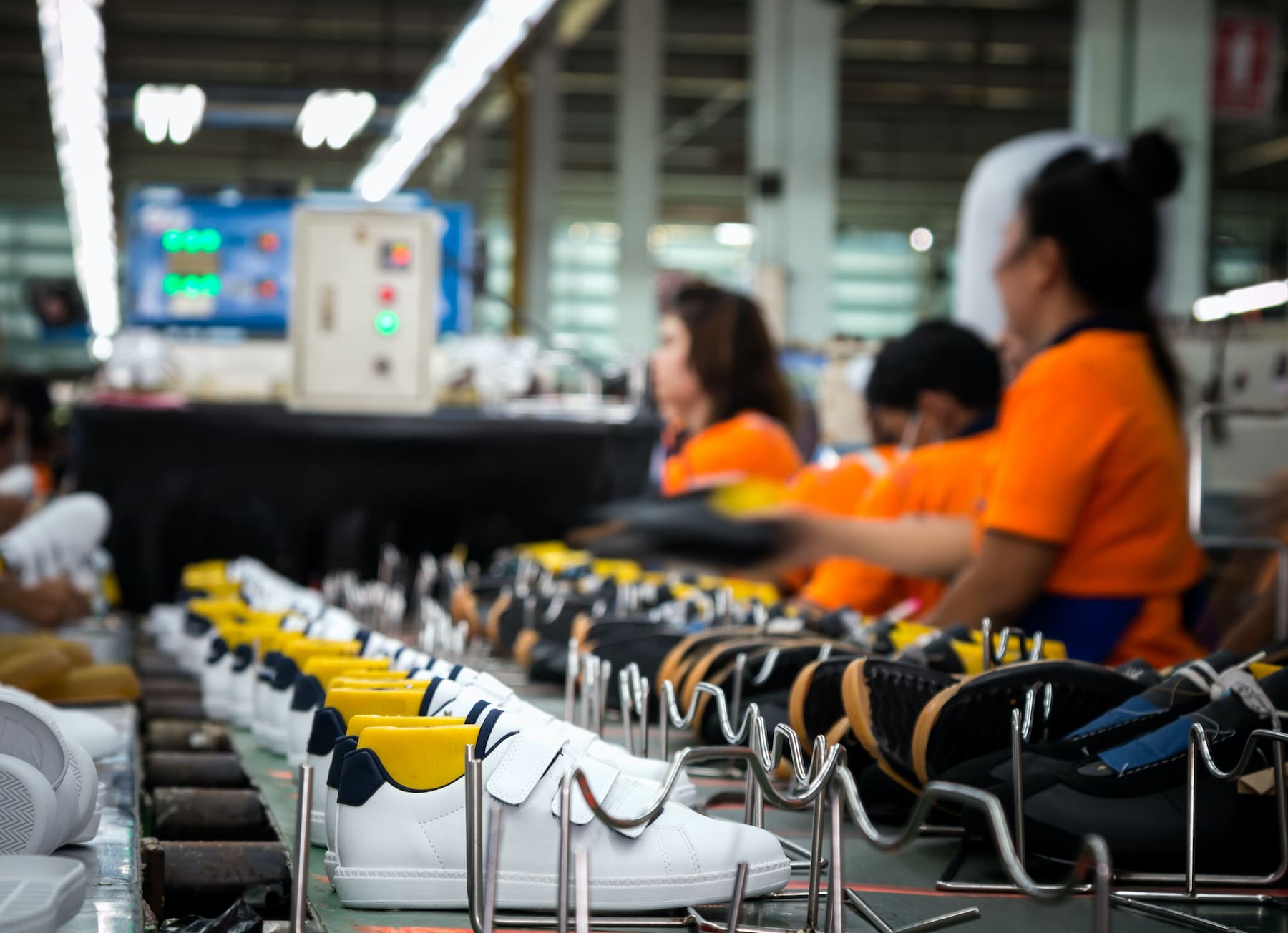
Featured Posts
-
White House Cocaine Incident Secret Service Wraps Up Investigation
Apr 22, 2025 -
Los Angeles Palisades Fire A List Of Celebrities Who Lost Their Properties
Apr 22, 2025 -
Wall Streets Flight To Safety Why Netflix Thrives In The Big Tech Downturn
Apr 22, 2025 -
Toxic Chemicals From Ohio Train Derailment Months Long Building Contamination
Apr 22, 2025 -
Selling Sunset Star Accuses Landlords Of Price Gouging Amidst La Fires
Apr 22, 2025