Understanding The Difficulties Of All-American Production
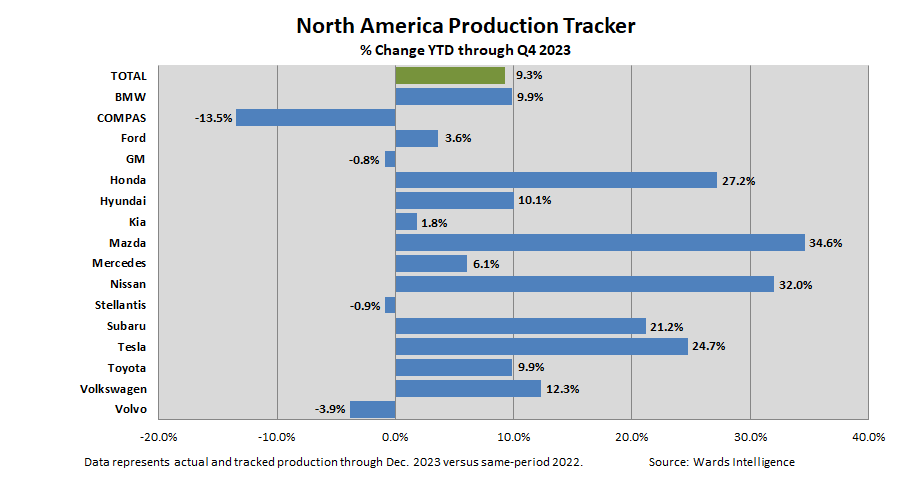
Table of Contents
High Labor Costs and Competition
The pursuit of all-American production faces significant headwinds due to the higher labor costs in the US compared to many other countries. This impacts price competitiveness and makes it difficult for domestic manufacturers to compete on a global scale.
Wages and Benefits
- Higher Wages: Average wages in the US, particularly in skilled manufacturing jobs, are substantially higher than in many developing nations. This directly increases production costs. For example, the average hourly wage for manufacturing workers in the US is significantly higher than in countries like China or Vietnam.
- Comprehensive Benefits Packages: US employers typically offer more comprehensive benefits packages, including health insurance, retirement plans, and paid time off, further adding to labor costs. These mandated benefits, while crucial for employee well-being, contribute to a higher overall cost structure compared to countries with less robust social safety nets.
- Impact on Manufacturing Costs: The combined effect of higher wages and benefits significantly impacts the final cost of goods produced domestically, making them less price-competitive in the global marketplace. This price difference can make it challenging to compete against imported goods, even with superior quality.
Global Competition
The US manufacturing sector faces intense competition from countries with significantly lower labor costs. This global competition presents a major obstacle to the growth of domestic manufacturers.
- Industries Heavily Impacted: Industries like textiles, electronics, and certain segments of the automotive sector have been profoundly impacted by this global competition. Many companies have shifted production overseas to take advantage of lower labor costs, leading to job losses in the US.
- Trade Agreements and Their Effects: International trade agreements, while aiming to foster global commerce, can sometimes exacerbate the challenges faced by domestic manufacturers. These agreements can lead to increased imports and put pressure on US companies to lower prices to remain competitive.
- Case Study: The Textile Industry: The US textile industry provides a prime example of the challenges posed by global competition. Many textile manufacturers have relocated their operations to countries with significantly lower labor costs, leading to a decline in domestic production and employment.
Supply Chain Challenges and Raw Material Sourcing
Another significant hurdle in achieving all-American production is the difficulty of sourcing all necessary raw materials domestically. This reliance on imports creates vulnerabilities and increases costs.
Domestic Sourcing Limitations
- Limited Domestic Resources: Many essential raw materials, such as certain rare earth minerals and specialized components, are either not produced in sufficient quantities in the US or not produced at all. This necessitates importing these materials, introducing both cost and logistical challenges.
- Impact on Lead Times and Costs: The need to import raw materials can significantly increase lead times and overall production costs. Shipping delays, tariffs, and currency fluctuations can all add to the expense and unpredictability of the supply chain.
- Companies Striving for Domestic Sourcing: Some companies are actively working to increase domestic sourcing, but this often requires significant investment in research, development, and establishing new supply chains. This process is lengthy and may not always be feasible or economically viable.
Transportation and Logistics
Domestic transportation, while crucial for all-American production, is often more expensive and less efficient than global shipping.
- Higher Fuel Costs: Fuel costs significantly impact transportation expenses. Fluctuations in fuel prices can create instability and unpredictability in production budgets.
- Infrastructure Limitations: The US infrastructure, while extensive, faces challenges in terms of capacity, efficiency, and maintenance. Congestion and outdated infrastructure can lead to delays and increased transportation costs.
- Impact on Timelines and Expenses: The combined effect of higher fuel costs, infrastructure limitations, and longer transportation distances can considerably impact production timelines and overall expenses, making all-American production less cost-effective in some cases. This is particularly true for bulk materials.
Regulatory Compliance and Environmental Concerns
The US has stricter environmental regulations and more complex bureaucratic processes compared to many other countries. These factors add to the cost and complexity of all-American production.
Environmental Regulations
- EPA Standards and Other Regulations: The Environmental Protection Agency (EPA) and other regulatory bodies impose stringent environmental standards on manufacturing processes. Compliance requires investments in pollution control technologies and sustainable practices.
- Investment Needed for Compliance: Meeting these environmental regulations can demand substantial upfront investments in equipment, technology, and processes. These investments can significantly increase production costs and reduce profitability.
- Impact on Profitability: The cost of complying with environmental regulations can be substantial, potentially impacting the overall profitability of domestic manufacturing operations and making it more difficult to compete with businesses in countries with less stringent environmental rules.
Bureaucracy and Permits
Navigating the US regulatory landscape, obtaining necessary permits, and complying with various licensing requirements can be a time-consuming and complex process.
- Time and Resources for Compliance: Businesses must allocate significant time and resources to ensure compliance with various regulations, potentially delaying project implementation and increasing administrative costs.
- Delays in Project Implementation: The bureaucratic hurdles associated with obtaining permits and licenses can significantly delay project timelines, hindering timely production and market entry.
- Examples of Regulatory Hurdles: Numerous examples exist of domestic manufacturers facing significant delays and added costs due to navigating complex permit applications and regulatory approvals. This bureaucratic complexity can be a major deterrent to domestic production.
Technological Advancements and Automation
To compete with lower-cost labor in other countries, US manufacturers must invest heavily in automation and technology. This requires significant upfront capital and ongoing maintenance.
Investment in Automation
- High Initial Costs: The initial investment in advanced automation technologies, including robotics and sophisticated machinery, can be substantial. This investment represents a significant barrier to entry for many businesses.
- Ongoing Maintenance: Maintaining and upgrading automated equipment requires ongoing investment in skilled labor and specialized parts, adding to the overall operational costs.
- Successful Automation Implementations: Despite the high costs, successful automation implementation can significantly increase efficiency and productivity in the long term, improving competitiveness and reducing labor costs in specific areas.
Skilled Labor Shortages
The US faces a significant challenge in finding and retaining skilled labor for advanced manufacturing jobs. This skills gap impacts production efficiency.
- Need for Training and Education: Addressing the skills gap requires investment in training programs and educational initiatives to equip workers with the necessary skills for advanced manufacturing roles.
- Competition for Talent: The competition for skilled labor is intense, with companies vying for the limited pool of qualified individuals. This competition can drive up wages and make it challenging to retain skilled workers.
- Impact on Production Efficiency: Skilled labor shortages can directly impact production efficiency and overall output, potentially hindering the ability of US manufacturers to meet market demands.
Conclusion
Achieving all-American production presents a multifaceted challenge. High labor costs, complex supply chains, stringent regulations, and the need for significant technological investment all contribute to a higher cost structure compared to manufacturing in many other countries. Understanding these complexities is crucial for informed decision-making. By acknowledging these challenges and proactively seeking solutions, businesses can work towards a more sustainable and successful "Made in the USA" approach. Further research into industry-specific challenges and innovative solutions is recommended to navigate the complexities of all-American production effectively.
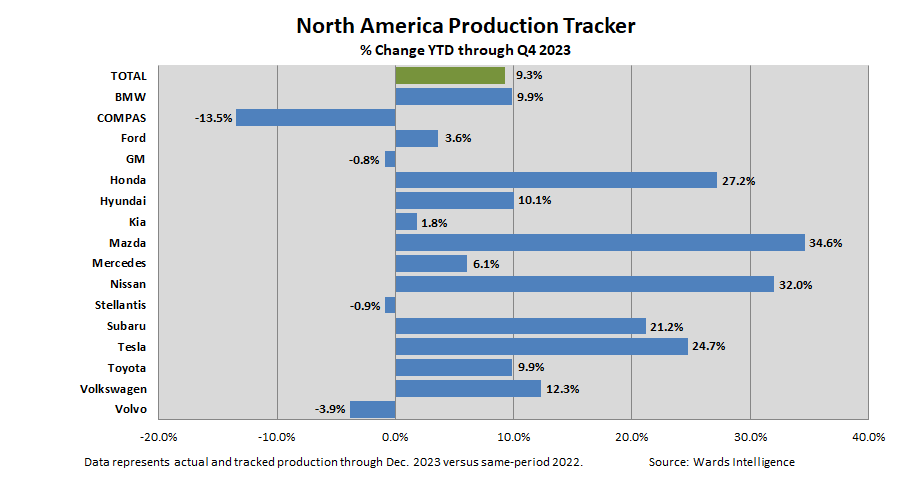
Featured Posts
-
Capital Summertime Ball 2025 Tickets Tips For Braintree And Witham Residents
Apr 29, 2025 -
Anthony Edwards Fined 50 K For Inappropriate Response To Fan Question
Apr 29, 2025 -
Analysis Of Trumps Promise Of A Posthumous Pardon For Pete Rose
Apr 29, 2025 -
Analysis Of Musks X Debt Sale Impact On Company Financials
Apr 29, 2025 -
Pete Rose Pardon Will Trump Overturn The Baseball Betting Ban
Apr 29, 2025